Our innovation is a direct result of our team’s vision and creative ideas
Stephenson Engineering knows that it takes more than steel and concrete to build a structure. It takes people who have a vision and ground-breaking technology to bring those ideas to life. Our team challenges the conventional while looking for more efficient, cost-effective ways of doing things, instead of using off-the-shelf solutions.
We use a collaborative approach, calling on the considerable talent, skill, and specialized knowledge of each of our team members. We design solutions based on real-world examples found in both the man-made and natural world. When fully realized through software platforms like Revit and CAD, our solutions always surpass the expectations of our clients.
Queen Richmond West Centre
MEGA DELTA FRAME – JACKS
The ability to preserve historic buildings while allowing for the construction of high-density development in urban environments is an important current issue in the industry.
The Queen Richmond Centre West is an example of the ability of the construction industry to balance heritage and development. This distinctive building in Toronto is a ten-storey office building floating above existing four and five-storey masonry and timber heritage buildings.
To support the building above, we created a unique “Mega Delta Frame” structure utilizing a central node of steel casting. The Mega Delta Frame can be visualized as two space frame pyramids stacked on each other with the upper one inverted such that the points of the two pyramids join at a central node.
The configuration of the structure enables the Mega Delta Frame to contribute to the lateral stiffness of the building under wind and seismic loading in addition to supporting the gravity loads of the columns above. The result of the “Mega Delta Frame” is a visually pleasing architecturally dynamic structure, that has become the signature of the building.
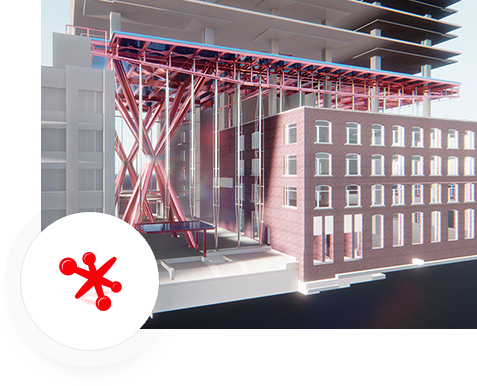
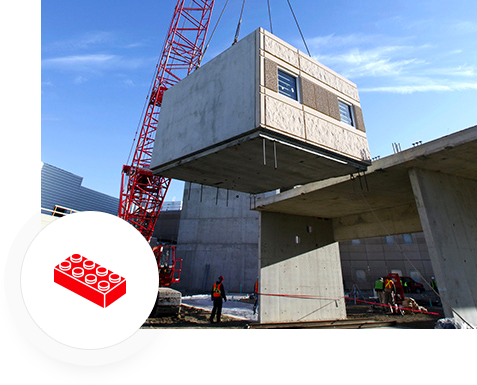
Toronto South Detention Centre
PRECAST CONCRETE BLOCKS
With the Toronto South Detention Centre, we were faced with the challenge of a large complex project with an extremely tight time frame for design and construction. Our solution to meet these demands was a precast concrete framed detention building utilizing precast cells, columns, beams, and floors. The precast cells act as an integral part of the building structure. To facilitate the repetitive nature of cells in a detention centre we utilized a precast system for the building structure. The cells were formed as six-sided boxes which were integrated into the building and became the building’s lateral and gravity bearing structure. The use of precast cells allowed for greater quality control versus cast-in-place concrete or masonry cells. This precast solution allowed for the off-site fabrication of components and significantly accelerated the construction.
Brampton Civic Hospital
THE ZIPPER SOLUTION
When constructing large institutional buildings that meet post-disaster criteria, conventional practice dictates the use of an expansion joint through the centre of the building, necessary due to the length of the building. In circumstances such as Brampton Civic Hospital where the design called for a 600foot long Inpatient Building, the proposed traditional expansion joint would have been approximately eight inches wide in all floors, walls and ceilings, as well as in pipes, ducts, conduits and gas lines.
Stephenson Engineering set a goal to determine a method that would eliminate this costly and unsightly requirement. Our team-based approach to problem-solving led to the development of what we have traditionally referred to as the “zipper.”
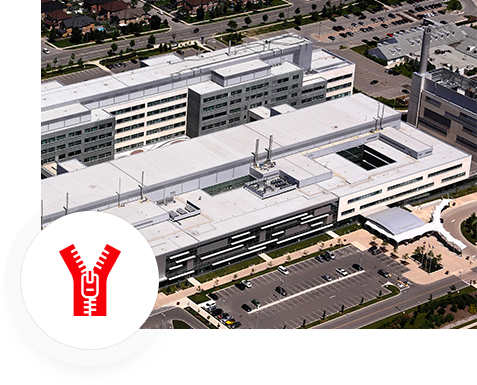